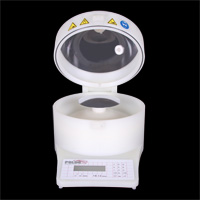
ACD 200
|
¥õ200
mmÀÌÇÏ
APT German |
1~10,000 rpm
Á¤¹Ðµµ : ¡¾1RPM
Digital
Acceleration
/Deacceleration 30,000rpm/s
N2 Purge
Port |
99½ºÅÜ
¼³Á¤ °¡´É
99memories
µðÁöÅÐ
Á¦¾î
AC200V
|
½ºÇÉÄÚÅÍ ¿ÜÇü
330w*310h*610d mm
¼ÒÇü*Ź»ó
ŸÀÔ
¸¶ÀÌÅ©·ÎÇÁ·Î¼¼¼ ȸÀü Á¦¾î
(ȸÀü, Á¤Áö, slope ¾÷, slope ´Ù¿î)
Digital LCD Coontrol
Safety Door Lock
Solution Æ¢±è ¹æÁö ¼³°è |
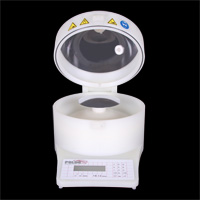
ACD 300 |
¥õ300
mmÀÌÇÏ
APT German |
1~10,000 rpm
Á¤¹Ðµµ : ¡¾1RPM
Digital
Acceleration
/Deacceleration 30,000rpm/s
N2 Purge
Port |
99½ºÅÜ
¼³Á¤ °¡´É
99memories
µðÁöÅÐ
Á¦¾î
AC200V
|
½ºÇÉÄÚÅÍ ¿ÜÇü
430w*315h*610d mm
¼ÒÇü*Ź»ó
ŸÀÔ
¸¶ÀÌÅ©·ÎÇÁ·Î¼¼¼ ȸÀü Á¦¾î
(ȸÀü, Á¤Áö, slope ¾÷, slope ´Ù¿î)
Digital LCD Coontrol
Safety Door Lock
Solution Æ¢±è ¹æÁö ¼³°è |
FEATURES ACD200-PTFE-HD Single Substrate Spin Etcher,Developer:
- ¿ÀÅä¸Þƽ ÄɹÌÄà µð½ºÆæ½º:
- dispensing fluids through up to 6 spray nozzles (2 standard included)
- each programmable for sequential or parallel dispense
- Clear/Transparant Domed Lid with central integrated N2 shower purge
- Seamless Full-Plastic Housing in High Chemical Resistant PTFE(TFM)
- Table-Top Model: dimensions:?33 (w) x?55 (d) x?32 (h) cm
- Substrate size: fragments and substrates up to ¨ª260mm (or 8") or 6"x6"
- Heavy-Duty Servo-Controlled Motor:
- Assuring repeatable rpm rates
- Rotation Speed Adjustable 1 to 10.000rpm
- Clockwise and Counterclockwise Rotation
- Puddle function for developer purposes
- Easy, step-by-step Programming via?Gloved-Finger-Friendly, Full-Size Keyboard with LED Backlit Display?
- Programmable Digital Process Controller:
- Storage of multiple programs of?99 Step Recipes each, for:
- Speed 1-10.000rpm, Time, Acceleration
- Vacuum On/Off?
- Relay Open/Close
- Multi-User Access Levels
- 2 Programmable ON/OFF Switching Outputs
e.g. for Dispense On/Off, Nitrogen On/Off, etc.
- Drain connection
- CE-approved
Unit comes standard?including 2 integrated spray nozzles and central N2 shower purge.?
Vacuum Chuck A-V36-S45-PTFE-HD and Small Fragment Adapter D-V10-S50-PTFE-HD up to ¨ª150mm, or alternatively, Vacuum Chuck A-V87-S96-PTFE-HD for larger substrates up to ¨ª200mm and (1) centering aid (F-Sx/POLOS200) are included.
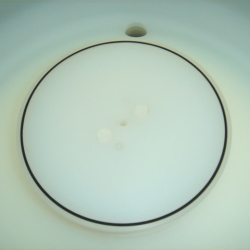
Adapter D-V10-S50-PTFE-HD,
A-V87-S96-PTFE-HD
easily fits on top of A-V36-S45-PTFE-HD
A wide variety of other chucks, including non-vacuum, are available at request.
Round Substrates
2" up to 300mm wafers
Non-Vacuum Chuck,
with centering pins.
Customized sizes at request.
|
Fragments/Die.
Fragment Adaptor, Vacuum 50mm centerhole
for use with A-V36-S45-PP Vacuum Chuck
|
Square Substrates
(Masks, Solar Cells, etc.)
Non-vacuum Chuck with centering pins.
Customized sizes at request.
with 6 centering pins,
without vacuum for 101.6mm (4") square substrates.
(Please specify substrate size in mm.)
|
Rectangular Substrates
(Laboratory Glass, etc.)
Recessed Vacuum Chuck.
Customized sizes at request.
Recessed Vacuum Chuck for rectangular substrates (e.g. Laboratory Glass):
(Please specify substrate size and thickness in mm.)
|
Low contact.
Non-vacuum Chuck with centering pins.
Customized sizes at request.
Low contact chuck
Thin, Fragile Substrates.
Vacuum Chuck
Customized sizes at request.
Vacuum Chuck for film or other thin substrates
The POLOS ACD200 Spin Processors are available?in NPP or PTFE, as Table-Top or OEM In-Deck unit.
OPTIONS
- OEM In-Deck Version (ID)
- Wafer Centering Tool
- Drain Exhaust Hose (DEXT)
- Drain Exhauxt Seperation Port Tee (DET)
- Vacuum Pump (VP80)
- Dispense Vessel in PTFE (DV)
- Adjustable Injector Head (ILACD)
- Back-Side Rinse (BSR)
- Edge Bead Removal (EBR)
- Mini Wet Station (MWS)
TYPICAL APPLICATION:
DRYING |
REQUIREMENTS :
- Use Low Contact Chuck
(non-vacuum chuck)
only the edge of the substrate is in contact with the chuck
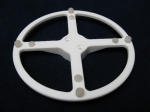
RECOMMENDED MODELS*:
Manual Dispense
- Up to 150mm: SPIN150-NPP
- Up to 200mm: POLOS MCD200-NPP
- Up to 300mm: POLOS MCD300-NPP
* Models are standard supplied with vacuum chuck , mechanical chucks are optionally available, depending on substrate.
CHECK CHEMICAL COMPATIBILITY OF YOUR PROCESS WITH THE NPP OR PTFE BOWL-MATERIAL .
PICTURE:
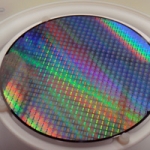
|
RINSE / CLEANING |
REQUIREMENTS:
- Choice of Vacuum or Non-Vacuum Chuck
- Manual (MCD) or Automatic Chemical Dispense (ACD)
OPTIONAL:
- Back-Side Rinse
(only with mechanical chucks)
RECOMMENDED MODELS:
Manual / Automatic Dispense
- Up to 150mm: SPIN150-NPP* / POLOS ACD200-NPP*
- Up to 200mm: POLOS MCD200-NPP* / ACD200-NPP*
- Up to 300mm: POLOS MCD300-NPP* / ACD300-NPP*
* Teflon¢ç (PTFE) units are available, depending on chemicals.
CHECK CHEMICAL COMPATIBILITY OF YOUR PROCESS WITH THE NPP OR PTFE BOWL-MATERIAL.
PICTURE:
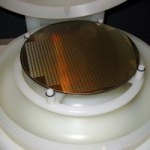 |
ETCHING: |
REQUIREMENTS:
RECOMMENDED MODELS:
- Up to 150mm: POLOS ACD200-PTFE-HD*
- Up to 200mm: POLOS ACD200-PTFE-HD*
- Up to 300mm: POLOS ACD300-PTFE-HD*
* These unit are suitable for Puddle Etch processes, speedrates can be set from 1 up to 7.000 rpm, chuck turning can be programmed to rotate alternating between clockwise and counter clockwise.
-
Puddle etching method of thin film by using spin-processor
The present invention discloses a puddle etching method of thin film.
In a spin etching equipment, pre-wet the wafer by D.I. water and etch solution to remove the contamination and the upper layer of the film on the wafer.
Then spin slowly (about 0-50 rpm) and inject etching solution to form a puddle of etching solution which will stay on the wafer, the wafer then keep spin slowly (about 0-50 rpm) such that the puddle of etching solution stay on the wafer and etching is going on by puddle etching.
After the thin film is etched, the wafer is spin at higher speed, and D.I. water is injected to rinse.
Then, IPA is used to remove the D.I. water by Marangoni effect.
Finally raise the speed to dry the wafer.
CHECK CHEMICAL COMPATIBILITY OF YOUR PROCESS WITH THE NPP OR PTFE BOWL-MATERIAL
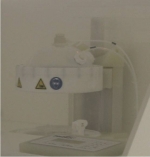
|
AUTOMATIC COATING |
A full range of substrate size matching vacuum or non-vacuum chucks is available, for easy centering.
OPTIONS:
- Centering Tool
- Drain Hose
- Top- and / or Backside Rinse
- Dispense Vessels
- Extra Injector Lines
RECOMMENDED MODELS:
- Up to 150mm: POLOS ACD200-NPP-HD
- Up to 200mm: POLOS ACD200-NPP-HD
- Up to 300mm: POLOS ACD300-NPP-HD
CHECK CHEMICAL COMPATIBILITY OF YOUR PROCESS WITH THE NPP OR PTFE BOWL-MATERIAL.
PICTURE:
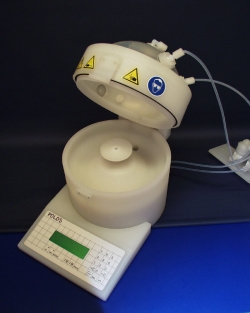
|
DEVELOP |
REQUIREMENTS:
- ACD Automatic Chemical Dispense
- Teflon(PTFE) Housing
- Exhaust / Drain Combination
- Dispense Vessel
OPTIONS:
A full range of substrate size matching vacuum or non-vacuum chucks is available, for easy centering.
- Centering Tool
- Backside Rinse
- Edge Bead Removal
- Additional Injector Lines
- Auto Lid-Lock
RECOMMENDED MODELS:
- Up to 150mm: POLOS ACD200-PTFE-HD
- Up to 200mm: POLOS ACD200-PTFE-HD
- Up to 300mm: POLOS ACD300-PTFE-HD
CHECK CHEMICAL COMPATIBILITY OF YOUR PROCESS WITH THE NPP OR PTFE BOWL-MATERIAL.
PICTURE:
Developing
Edge bead Removal
Edge bead removal spray nozzle (topside substrate) with adjustable position, including standard nozzle
Backside spray nozzle with adjustable position for rinsing of chuck side of substrate, including standard nozzle.
Spin processing is widely used in the semiconductor industry, where spin coating can be used to create thin films of less than 10nm thickness. ?Spin processing can be used for cleaning or etching. ?Most substrates can be spin processed, including wafers, microscopeslides, photomasks, or even small pieces etc.?
Our spin processors are?used intensively inboth cleaning applications and forphotolithography, to deposit layers of photoresist typically 1 micrometer thick. Photoresist is typically spun at 1000 to 4000 revolutions per minute for 30 to 60 seconds to achieve uniformity. ?Our spin processors are?available for all sizes, ranging from small pieces to large 1000mm diameter substrates
|
PICTURE:
?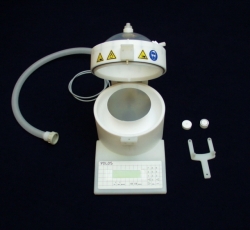
Teflon is a Dupont registered trademark. TFM is a Dyneon registered trademark.
- Available Standard Spray Nozzles
|
|
Hhigh quality spin coated
layers °¡ ÇÊ¿äÇÑ ºÐ¾ß:
- Photoresist for defining patterns in microcircuit fabrication.
- Dielectric/insulating layers for microcircuit fabrication ? polymers,
SOG, SiLK, etc.
- Magnetic disk coatings - magnetic particle suspensions, head lubricants,
etc.
- Flat screen display coatings. - Antireflection coatings, conductive
oxide, etc.
- Compact Disks DVD, CD ROM, etc.
- Television tube phosphor and antireflection coatings.
11
°æ±âµµ
¾È¾ç½Ã µ¿¾È±¸ È£°è555-9
¾È¾ç
±¹Á¦ À¯Å뽺ÅÜÁö 17µ¿ 127È£
Tel
: (031) 479-4211/2, Fa* : (031) 479-4213
1992-2001
,Jaesung ITS ,co. All rights reserved
Contact
us : jsi@jsits.com |